Die-casting is the cost effective way of manufacturing wide range of components. In this process molten metals are forced into the mold cavities of the die casting machines. The
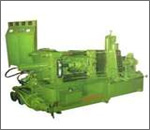
highest volume of casting in the metal casting industry is made in this method.
Design: There are two halves for the die casting machine - the fixed half and ejector. Both the haves are closed tightly by hydraulic pressure during the casting process. After the completion of the casting process the casts are removed through the ejector die half. The surface are of the cast is calculated by the die parting line which is the meeting point of the two parts of the mold.
Nowadays, special casting features like sprues, runners, gates, etc are also fixed to the mould. Before finalizing the design it is essential that the designers consult with the die caster, because that will help in understanding the requirements and the limitation of the die machine.
Advantages of Die Casting Machines:
- Effective is casting complex components with dimensional accuracy
- The process is economical provided proper tooling and casting techniques are employed
- Minimal or no machining required
Types of die casting machines:
- Cold Chamber Die Casting Machines
- Hot Chamber Die Casting Machines
There are Four Types of Dies used in Die Casting Machines:
- Single cavity to produce one component
- Multiple cavity to produce a number of identical parts
- Unit die to produce different parts at one time
- Combinations die to produce several different parts for an assembly
Types of Die Casting Process: Hot Chamber Machines: Hot chamber machines are used primarily for zinc, copper, magnesium, lead and other low melting point alloys that do not readily attack and erode metal pots, cylinders and plungers. The injection mechanism of a hot chamber machine is immersed in the molten metal bath of a metal holding furnace. The furnace is attached to the machine by a metal feed system called a gooseneck. As the injection cylinder plunger rises, a port in the injection cylinder opens, allowing molten metal to fill the cylinder. As the plunger moves downward it seals the port and forces molten metal through the gooseneck and nozzle into the die cavity. After the metal has solidified in the die cavity, the plunger is withdrawn, the die opens and the casting is ejected.
High Integrity Die Casting Methods: There are several variations on the basic process that can be used to produce castings for specific applications. These include Squeeze casting, a method by which molten alloy is cast without turbulence and gas entrapment at high pressure to yield high quality, dense, heat treatable components.
Applications of Die Casting Machines: Die castings provide integral fastening elements, such as bosses and studs. Holes can be cored and made to tap drill sizes, or external threads can be cast.
The die casting method is especially suited for applications where a large quantity of small to medium sized parts is needed with good detail, a fine surface quality and dimensional consistency.