Abrasion resistant casting or wear resistant castings are resistive to abrasion and wear & tear, which is accomplished by using specific abrasion resistant metals and bi-metals, respectively. Abrasion resistant casting products
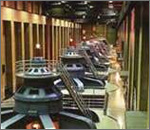
take shape by the successive pouring of low alloy steel and white cast iron. The duo-cast product abrasion resistant casting exhibits wear resistance several times higher than conventional wear resistant materials. Abrasion resistant castings are created in white iron or chilled iron with nickel, chrome and moly additives. Abrasion resistant castings are ideal for applications demanding simultaneous dual functionality such as wear-resistance and impact-resistance.
Abstract Superior abrasive wear resistance, combined with relatively low production costs, makes high Cr white cast irons (WCIs) particularly attractive for applications in the grinding, milling, and pumping apparatus used to process hard materials. Hypoeutectic, eutectic, and hypereutectic cast iron compositions, containing either 15 or 26 wt pct chromium, were studied with respect to the macrostructural transitions of the castings, solidification paths, and resulting microstructures when poured with varying superheats. Completely equiaxed macrostructures were produced in thick section castings with slightly hypereutectic compositions. High-stress abrasive wear tests were then performed on the various alloys to examine the influence of both macrostructure and microstructure on wear resistance. Results indicated that the alloys with a primarily austenitic matrix had a higher abrasion resistance than similar alloys with a pearlitic/ bainitic matrix. Improvement in abrasion resistance was partially attributed to the ability of the austenite to transform to martensite at the wear surface during the abrasion process.
The effect of the temperature and time of the destabilization and sub-critical heat treatments on the abrasive wear behaviour of two high-chromium white iron alloys (15-3 Cr---Mo a
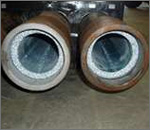
nd 27 Cr) was investigated. The response of each alloy to the destabilization heat treatment and, therefore, the micro-structures developed, differed significantly. Pin abrasion tests were conducted, and showed the wear resistance of the 15-3 Cr---Mo alloy to be superior to that of the 27 Cr alloy for most conditions.
Following abrasion testing, retained austenite measurements using X-ray diffraction and microhardness measurements on the wear pins indicated the extent of austenite transformation and work-hardening. The work-hardening due to abrasion was greater for the 15-3 Cr---Mo alloy and this was related to the difference in composition of the matrix of each alloy. Abrasion on garnet and on alumina produced similar levels of work-hardening for both alloys, despite the differences in the abrasive hardness. Sub-critical heat treatments increased the abrasive wear loss. In particular, the formation of ferrite/carbide aggregates during the sub-critical heat treatment greatly increased the wear rate.
Contact us to buy or for more information on abrasion resistant casting process, advantages of abrasion resistant castings, abrasion resistant castings, wear resistant castings, uses of wear resistant casting.