Introduction: In recent years, the cold box process has become increasingly popular in the Indian. foundry industry. Many foundries
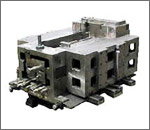
already use this coremaking process, or are interested in doing so. Instead of baking the mold is binded and strengthened by chemically adhering to the sand. They get their name for not being baked. They give more accurate results but are more expensive than green-sand molds. Being used since the second half of the 1960's this process is widely used for gray iron, nodular iron and steel casting sector. This process was improved with the introduction of humidity resistance cold box system in the 1970's which enabled the used of water based coatings.
Cold Box Casting Process: The sand molding matrix is of special significance in the cold box process. The economy of the process and quality of the castings to be produced depend to a critical extent on the sand being used. In principle, all refractory matrices used in the foundry industry can be employed for the cold box process. These essentially represent silica sand, chromite sand and zircon sand.
Working with the cold box process requires resin, activators, catalyst and refractory matix components. Coreboxes for the cold box process may be manufactured from various materials including Wood, plastic, Aluminum, Grey Iron, Steel, etc. The selection of a construction material depends on the number of cores to be produced in the corebox. Combinations of wood and plastic, or better of aluminum and plastic be used as corebox materials in a jobbing foundry with lot sizes of 20 to 1000 cores. In selecting the plastics for use in corebox construction, plastic must be resistant to the components used in the cold box process. The second most important consideration in core production is the design of the corebox.
Applications: high volume cores in both ferrous and non-ferrous foundries.
Advantages:
-
Problem-free stripping of cores from the corebox
- Minimization of the resin buildup in the corebox
- Reduction of catalyst consumption
- Productivity increase
- Avoidance of casting defects such as erosions and scabs due to the high thermal resistance of the new Cold Box Systems