Introduction: Lost foam casting technique (LFC) is known by different generic and propriety names like lost foam, evaporative pattern casting, evaporative foam casting, full mold, etc. Similar
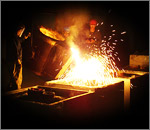
to the full mold process, in this process the pattern evaporates when the metal is poured into the mold.
Originally, full mold process was referred to as Lost Foam Casting . But, later the two processes were clearly differentiated by the use unboned dry silica in LFC while bonded sand was used in full mold process. This process gained world famous, when General Motors first implemented it to manufacture 4.3L, V-6 diesel cylinder head, in 1981.
Process: Lost foam casting is a type of metal casting process that uses expendable foam patterns to produce castings. Expanded polystyrene foam is used which melts when molten metal is poured into the mold.
Firstly, a pattern is made from form using a variety of methods. For small volume runs the pattern can be hand cut or machined from a solid block of foam, if the designs are simple enough it can even be cut using a hot-wire foam cutter.
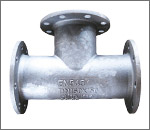
If the volume is large, then the pattern can be mass-produced by a process similar to injection molding. Pre-expanded beads of polystyrene are injected or blown into a preheated aluminum mold at low pressure. Injecting steam into the tooling cavity expands the beads. The beads will flatten against the tool surface and stick to one another. After cooling, the pattern is ejected from the tool. The final pattern is approximately 97.5% air and 2.5% polystyrene. Secondly, pouring basins, runners, and risers can be hot glued to the patter to form the final pattern assembly. The assembly is then coated with refractory coatings, which prevents the sand mold from breaking during the casting process.
Finally, when the coating dries, the cluster is placed into a flask and surrounded with un-bonded sand. Sand is compacted around the pattern by vibrating the table. Molten metal is poured into this tight mold either mechanically or using automatic pouring machine. No flash is formed, since there is no draft or parting line is used.
Application: Lost foam casting is used mostly for automotive applications. Cast iron, aluminum alloys, steels, nickel and in some cases stainless steel and copper alloys are cast in this process. The flexibility of LFC is useful in making complicated casting assemblies for automotive parts like cylinder heads, weldments, etc. This simple and inexpensive method is used in hobby foundry work.
Advantage:
- A simple and affordable technique that can be used in home foundries
- Cleaning cost is reduced in lost foam casing
- Tooling used for the casting process does not wear away
- Complex shapes can be cast in near net shapes
- A Simple and inexpensive method for casting complex constructions
- Difficult designs can be done which in unattainable using other casting techniques
- Castings requires minimal machining
- Castings are dimensionally accurate with excellent surface finish.