Introduction: Plaster mold casting is a casting process where instead of sand, plaster of Paris is used as the molding aggregate. This expendable mold process plaster is used only for castin
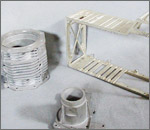
g non-ferrous metal for a wide of shapes and sizes, Plaster mold casting, also called rubber plaster molding (RPM), is a relatively economical process and therefore the foundry industry is working on to use plaster mold casting with investment casting.
The metal casting industry in on the look for more technical and economically viable casting process. For which many casting process are being combined to manufacture complex designs that require cope and drag mold. Of now no process has been able to replace the expensive investment casting method in the steel casting industry. But it is assumed that in future some complex, cost-effective casting technique is evolved in which plaster mold process is used.
Process: For the plaster mold casting metal pattern are used because wood patterns are difficult to be drawn from the mold. However, rubber pattern are used for complex geometrical designs. Before covering the pattern with the mold it is coated with some substance which will prevent the plaster from sticking to the pattern.
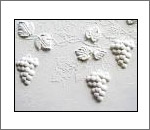
In plaster mold casting the pattern is place is a flask and plaster is poured over the pattern. The unit is shaken so that the plaster penetrates into every small cuting and designs made inthe pattern. When the pattern sets, the mold is baked so that the plaster mold becomes hard. The dried mold is then assembled, preheated, and the metal poured. Finally, after the metal has solidified, theplaster is broken from the cast part. The used plaster cannot be reused.
Molding aggregate in made of plaster and sometimes rubber. Plaster is mixed other constituent of achieve a creamy pouring consistency. The high insulating value of the plaster allows castings with thin wads to be poured. Additives are added to improves green strength, dry strength, permeability and castablity. The ratio of ingredients is 70�80% gypsum and 20�30% additives. the patterns is held in a flask. A few of the additives and their uses are as follows:
Talc or magnesium oxide |
prevent cracking and reduce setting time |
Lime and cement |
limits expansion during baking |
Glass fibers |
increase strength |
Sand |
used as a filler. |
Applications of Plaster Mold Casting: Parts that are typically made by plaster mold casting are lock components, gears, valves, fittings, tooling, and ornaments. Lock components, gears, valves, fittings, tooling, and ornaments. Also useful for prototypes and short run production of aluminum and zinc parts.
Applications:
- Reproducible casting process where fine detailing and close tolerance in maintained all the times
- In prototypes appearance and physical properties are maintained
- Casting have excellent surface finish and fine detailing
- Cost-effective casting process for complex components
- Reduced wastage of scrap materials.