Introduction: Rotational casting or
rotocasting is the other name for centrifugal casting. In rotocasting, the mold rotates on its axis while the metal solidifies in the seamless mold.
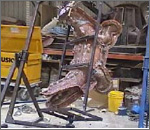
Rotocasting is used, for small quantity and small applications, to manufacture hollow items using metals and plastics. This is a relatively cheap process since, other than the rotation, no external pressure is required for the casting purpose.
Process: Rotocasting process involves a number of steps from the creation of a functional design to the final cleaning, inspection and polishing of the process. Generally, permanent molds made of steel, cast iron or graphite is placed on a horizontal or vertical axis. The mold are seamless and rotates with its axis mechanism. Expendable, sand molds can also be used. The walls of the mold are first coated with some refractory materials and baked. Once the mold is dried, it is rotated on its axis according to the speed required for the specific casting process. Now, molten metal is introduced directly into the mold, without using gates or sprues.
The mold continues to spin with the metal in it. Centrifugal force pulls the molten metal towards the centre. The molten metal nears the wall cools faster and moves to the inner parts of the mold. The impurities are also driven to the inner part of the mold. Therefore, the hollow castings created using rotocasting technique has to be sand blasted or machined to remove the impurities from inside. When the metal has solidified completely, the machine is stopped and the casting removed from the mold.
Application: Rotocasting or centrifugal casting is used to produce hollow objects for application in aerospace, industries, marine, and power transmission. Ferrous metals such as low alloy steel, stainless steel, and iron, or non-ferrous alloys such as aluminum, bronze, copper, magnesium, and nickel can be casted using this process. Some of the asymmetrical component that are produced are cylinders or disks, bearings, bushings, coils, cylinder liners, nozzles, pipes, tubes, pressure vessels, pulleys, rings, and wheels.
Advantage:
- Rotational molding can achieve seamless product surface with relative cheap molds
- Hand or machine mix can be done
- Casting of various densities and properties can be done.